Evaluating community science sampling for microplastics in shore sediments of large river watersheds
Abstract
A community science project in the Ottawa River Watershed in Canada interacted with an existing volunteer base to collect sediment from 68 locations in the watershed over approximately 750 km. Ninety-one percent of the distributed kits were returned with 42 volunteers taking part in the project. After analysis, particle concentrations were relatively low compared to previous freshwater microplastic sediment research, with contributing factors including (but not limited to) the large size of the watershed, a lower population base compared to other researched freshwater watersheds, the relative size and discharge of the Ottawa River and the large seasonal fluxes experienced in the river basin. Utilising community science for sampling large freshwater watersheds demonstrated its advantages in the research, especially spatially. However, careful consideration to research design and implementation is essential for community science projects examining microplastics in freshwater sediments. Research teams should ensure they are responsible for strict quality assurance and quality control protocols, especially in the laboratory with sample preparation and processing. Nonetheless, community science is potentially an extremely useful approach for researchers to use for microplastic sampling projects over large spatial areas.
Introduction
Microplastics have become a global concern and have been identified from the highest point on the globe (Napper et al. 2020) to the deepest ocean trench (Peng et al. 2018). Microplastics are defined as plastic pieces less than 5mm (Masura et al. 2015) and can be classed as either primary microplastics, manufactured at this micro-scale, or secondary microplastics that have fragmented from larger plastics. Microplastic pollution continues to increase at alarming rates and now is considered the primary constituent of marine debris (Moore 2008; Barnes et al. 2009; Cole et al. 2011). As microplastics are small, they are considered bioavailable to various organisms, thus have the potential to sorb and (or) release toxic chemicals, with potential transfer through the food chain (Reisser et al. 2014; Hurley et al. 2017). To date, a larger proportion of microplastic research has focused on the marine environment, however, increased attention has been given to freshwater systems, especially rivers that have been identified as the major conduit of plastics to marine areas with between 1.15 and 2.41 million tonnes of plastic waste entering oceans via rivers annually (Lebreton et al. 2017). With only limited microplastic research in freshwater systems, approximately 4% compared to marine research (Wagner and Lambert 2018), and with even less microplastic research focused on Canadian river systems (Castañeda et al. 2014; Vermaire et al. 2017; Forrest et al. 2019; Crew et al. 2020; Bujaczek et al. 2021) it is important to increase the scope of microplastic research in freshwater systems to enhance the understanding of microplastic inputs, outputs and sinks throughout freshwater watersheds. Microplastic concentration in river systems can be highly variable both spatially and temporally, indicating that researchers are only at the early stages of understanding these mechanisms (Forrest et al. 2020).
Community science is a potential technique to expand spatial monitoring for microplastics, especially across large project areas. Community science can be defined as scientific research and monitoring whereby members of the public collect, categorise, transcribe or analyse scientific data (Bonney et al. 2014). However, very few microplastic projects have adopted this approach to data collection. As with microplastic research in general, initial community science projects were focused on the marine area, including the International Pellet Watch (IPW) and community science projects monitoring for the plastic ‘nurdle’ (Tunnell et al. 2020). It can be assumed that freshwater community science microplastic monitoring is still being evaluated as a valid complementary research tool (Forrest et al. 2019), nevertheless, it has been applied previously at the watershed scale examining microplastics in river water (Barrows et al. 2018; Forrest et al. 2019). Previous research in the Ottawa River determined that for community science projects, larger volumes of water were required to gather representative microplastic counts in river water (Forrest et al. 2019), thus, an easier approach to community science as a spatial research tool was to evaluate the collection of beach sediments that are more easily accessible and potentially contain a greater concentration of microplastics.
Community science has been criticized and not necessarily accepted as a valid method of scientific investigation, with papers containing community science components traditionally finding difficulty in publication acceptance (Bonney et al. 2014). Concerns arise due to potential error, bias, reliability of data collection or concerns over the data quality (Burgess et al. 2017), as well as the lack of appropriate protocols, training, or oversight. There are also concerns of replicability, comparability, and completeness of the data contributed by volunteers. Subsequently, Community Scientists, and (or) their data are often not considered in management decisions (Conrad and Hilchey 2011; Gillett et al. 2012). However, community science can present substantial benefits (Conrad and Hilchey 2011) and future microplastic research should strive to incorporate community science, particularly when larger spatial scales are involved (Bergmann et al. 2015).
The objective of this research was to work with Community Scientists to collect near-shore river sediments for the analysis of microplastics at the watershed scale. In addition, we evaluated the potential of community science collected samples as a viable complementary spatial analysis tool for microplastic research in freshwater systems.
Study region
The Ottawa River is a designated heritage river in Canada due to its cultural, economic and ecological importance. The river is considered the major tributary of the St. Lawrence River, and flows from its headwaters at Lac des Outaouais in Quebec, Canada, to Lake of Two Mountains (Lac des Deux Montagnes), near Montreal, Quebec, approximately 1 272 kilometers in length (Fig. 1). The Ottawa River watershed is large with an approximate area of 146 000 km2 (greater than the area of England) making it difficult for single research or monitoring teams to collect representative samples from the watershed. The average flow of the Ottawa River, measured at the Carillon Dam (approximately 30 kilometers upstream of the terminus) is 1 950 m3/s, with daily minimum recorded at 306 m3/s in 1971 and a maximum daily flow of 9 217 m3/s in 2019 (Ottawa Riverkeeper 2021).
Fig. 1.

The community science network
The group of volunteers who participated in the community science project come from an established volunteer network through the non-governmental organization Ottawa Riverkeeper, who participate in monitoring various river water quality indices throughout the watershed including tributaries of the Ottawa River. With such an expansive watershed, this volunteer base, known as the ‘Riverwatchers’, increases the spatial scope of monitoring various pollution indicators and have previously contributed community science work monitoring microplastics in river water (Forrest et al. 2019). Additionally, members of the Riverwatch network have ties to other volunteer and community networks that in turn can increase the spatial reach of the research. For example, some additional groups and community members who took part in the sampling along with a Riverwatcher Community Scientist included school classes, community centre groups, a rafting club, as well as interested youth participants.
Methodology
A total of 47 sediment sampling kits were distributed to Community Scientists. Sampling kits were handed to the Community Scientists in May 2019, after the Ottawa River freshet. Once the Community Scientists received the kits, they were free to sample during the late spring and summer period of 2019. Sample dates from the received sediment were between June and September (inclusive) of 2019. Each kit consisted of three containers for three bulk sediment samples, a paper 250 millilitre (mL) cup, and a bright pink string. Additionally, each kit contained an instruction sheet, and all materials were contained in a post-paid box addressed to the Aquatic Ecosystems and Environmental Change Laboratory address at Carleton University in Ottawa, Canada (Fig. 2). The kits were handed out during an information session where the aims and desired protocols of the project were conveyed to the volunteers. Sampling procedures were based on the sampling protocol in Horton et al. (2017). Four 250 mL grab samples were collected at one-metre intervals parallel to the shoreline. The research team indicated the optimal place to sample the shoreline was at a distinctive debris line on the shore, where the river level would have been before receding. The Community Scientists used the container, the length of rope (coloured bright pink to distinguish any possible contamination in the processing of samples) and a paper cup that held approximately 250 mL of sediment, for four collections pertaining to a 1 L bulk sample for one of the containers. The rope was pre-marked indicating one metre intervals, thus the volunteers collected one sample at the end of the rope, then at each of the two one-metre marks, and finally at the other end of the rope, representing the four 250 mL collections. Additionally, the rope had metal nails at each end to hold it in place during collection.
Fig. 2.

Community Scientists were asked to use their own trowel for the sediment collected and it was suggested that it was a metal trawl if possible. Each Community Scientist was provided with three containers and given the option to sample one location (utilising one to three of the containers), or at three different locations. The Community Scientists filled out the provided information sheet that included their name, GPS coordinates, location name, description of the sediments, and clothing colours worn during sampling. The Community Scientists then packed the bulk sample into the aforementioned pre-paid postal box and sent the sample to the laboratory where it was stored in a dark fridge for processing.
The research team trialed the sampling protocol at various shorelines in the Ottawa River watershed to test the methodology, including laboratory processing and analysis, as an evaluation before presenting the protocol to the Community Scientists (Figs. S1 and S2).
Additional analysis included exploring significance between urban and non-urban area concentrations, comparing lake areas to higher flow sections of the river, and comparing between the main channel and tributaries. Various t-tests were performed to establish any significance between these variables.
Laboratory analysis
Sediment preparation and density separation were based on the oil extraction protocol (OEP) (Crichton et al. 2017), with some modifications to adjust for processing times due to the large amount of sediment. The OEP was chosen as it uses canola oil as reagent, whereas other density separation techniques use harsher chemicals. For example, though zinc bromide (ZnBr2) has demonstrated the ability to extract higher density polymers, up to 1.7g cm−3 (Prata et al. 2019), canola oil’s lower toxicity was a factor in selection as ZnBr2 may pose a threat to health or the environment if mismanaged (Mani et al. 2019). Additionally, canola oil does not typically react with the fibres, thus there should be no changes to the structure and (or) the colour of fibres during density separation. Furthermore, an additional advantage of canola oil is cost, especially for larger projects, where it can become an important factor. For example, sodium iodide (Nal) can be an effective additive for density separation, separating plastics up to 1.6g cm−3, however, where canola oil may cost approximately $0.96 Canadian dollars (CND) per sample (Crichton et al. 2017), Nal can cost approximately $90.00 CND per sample and ZnBr2 approximately $922 CDN a sample (Crichton et al. 2017). Another commonly used reagent for density separation is sodium chloride (NaCl), which can be as cost effective, approximately $10.00 CDN a sample (Crichton et al. 2017). However, NaCl typically only recovers lower density plastics, up to 1.2 g cm−3 and could lower recovery rates significantly for environmental samples (Prata et al. 2019). Furthermore, some of the brine solutions for density separation are based on the specific density of the solution, therefore, exclude certain polymer types with higher densities such as Polytetrafluoroethylene (PTFE) (Lechthaler et al. 2020). Recent testing on canola oil has highlighted the capability of extracting microplastics in the density range from 11–1760 kg m−3 and in the size range from 0.02–4.4 mm (Lechthaler et al. 2020).
An additional factor to consider for density separation for larger projects is processing time. Comparatively, the OEP has a relatively short processing time when compared to other extraction procedures. For example, the OEP does not retain high amounts of organic material, whereas other reagents such as calcium chloride (CaCl2) requires overnight settling due to higher amounts of organic material that requires longer settling times (Stolte et al. 2015). Laboratory tests do confirm good recovery for the OEP, with an average recovery rate of 96.2% (± 2.2%) (Crichton et al. 2017). Additionally, other oil extraction protocols, for example castor oil (Mani et al. 2019), also exhibit good recovery rates in laboratory tests (99% ± 4%). However, when oil extraction protocols are applied to some environmental matrices, recovery rates may decline. For example, the castor oil protocol recovery rates drop to approximately 75% (± 13%) when used on riverine suspended solids (Mani et al. 2019). Nonetheless, Crichton et al. (2017) did apply the OEP validation by spiking beach samples of various grain sizes to try and represent real word conditions for extraction, rather than examining efficiency rates purely on laboratory testing.
Each sample was prepared under a laminar flow hood, transferred to a metal tray, and covered with foil before being transported to an oven for drying. Each sediment sample was dried in an oven at 70 °C (Corcoran et al. 2015), which is considered to be below the melting point of all common polymers. Furthermore, 70 °C would not provide conditions that could alter the inherent shape of polymers that may be in the sample (Kalpakjian and Schmid 2008). Drying times were between 6 and 72 h, dependent on the moisture levels of each received sample. Once a sample was dried, a dry weight of the sample was calculated and transferred to a laminar flow hood for density separation.
The samples received were a variety of grain sizes (it was stipulated in the presentation to the Community Scientists, an ideal sediment size range), thus, the first step after drying and before density separation was to put the sample through a 2 mm sieve and 1 mm sieve, with visual inspection for particles after each sieving. The canola oil was prepped for analysis by filtering it through a 100-micron mesh, to remove possible contamination within the canola oil vessel. For density separation, 100 g of the (dry) sediment sample was placed in a 500 mL beaker. Two hundred millilitres of deionized water were then added to the beaker. A clean glass stirring rod was used to swirl the water to create a vortex, so the entire sediment fraction was submerged in the water. After a short settling period, 10 mL of filtered canola oil were added to the beaker and the sediment stirred vigorously for 30 s so the canola oil would come into contact with the entire sediment fraction. The mixture was then left to settle until the oil layer separated fully to the top of the water. Once separation was completed, the oil and water were decanted from the sediment into a separatory funnel. The beaker sidewalls were then rinsed to dislodge any particles and the water and oil layer decanted again into the separatory funnel. The above process was repeated until the separatory funnel was three quarters full, then shaken vigorously for 30 s to ensure any plastics dislodged during decanting were re-introduced back into the oil layer. The mixture was then left to settle until the oil and water layers separated. Once settling was complete, the oil layer with plastic particles was retained and the water and sediment layers were released and discarded. The oil layer was then emptied into a vacuum filtration system with an 80-micron pre-inspected mesh. The filters were then backwashed into a petri dish and the filter and petri dish contents examined for microplastics under a stereomicroscope. Identified particles were then separated into fragments and fibres, and the colours of each fragment and fibre were noted.
Quality control and quality assurance
During sediment sample processing, a total of nine laboratory blanks (beakers filled with DI water) were placed in various locations under the laminar flow hood during processing, to account for the potential of airborne contamination in the laboratory. These controls averaged 0.78 fibres per blank, with the greatest concentration being three fibres in a single control sample. The Community Scientists were not asked to conduct field controls, as it would have complicated the sampling procedure. A previous community science project in the Ottawa River watershed noted that even with detailed and concise sampling protocol sheets and sampling methodologies that are presented thoroughly to the Community Scientists, the chance for errors in sampling, especially conducting controls, is higher with volunteers (Forrest et al. 2019). Instead, the detailed sample sheet included information on clothing type and colours to determine potential contamination, and it was expressed to the volunteers during the methodology presentation to try and limit the exposure time of the containers as much as possible to reduce the potential of airborne contamination in the field. Additionally, as the postage boxes were limited in size, the research team chose to include a third sampling container rather than an empty container that could have been a control. The research team noted the colour of clothing worn by the volunteers while processing the specific samples at the laboratory and did not count fibres of the same colour if they were extracted from the sample.
Results
Of the 47 distributed kits for sediment analysis, a total of 43 were returned, representing a return rate of 91%. There was a total of 42 volunteers who submitted a total of 68 locations in the Ottawa River watershed (Fig. 1). Of the samples received, two samples were discarded (one sample contained only sticks, leaves, and other dry material without sediment, while the other sample was damaged when received at the laboratory). Thus, 95% of the samples received were analysed. The distance between the most upstream and downstream locations was approximately 750 km. There were 56 locations sampled on the main channel of the Ottawa River with 12 locations on tributaries. These locations included five samples on the Gatineau River, one location on the Rideau River, one location on the Madawaska River, one location on the Bonnechere River, two locations on the Kipawa River, and two locations on the Kinojévis River. The largest concentration of samples received were centred in or close to the Ottawa/Gatineau urban area.
Approximately 101 kg dry weight of sediment was received in the laboratory. Of the sediment received, the average dry weight of the samples was 1.5 kg. Of the suspected microplastic particles observed from the samples, 77% were fibres and 23% were fragments. Of the fibres observed, the most common were blue (approximately 69% of the fibres), green 16%, red 5%, and black 4%. The main fragment colours were blue at 39%, white at 37%, and clear at 20%.
All of the samples received contained suspected microplastics and (or) anthropogenically modified fibres. For the concentration of identified particles, the overall average concentration was 0.06 particles per 100 g of dry weight (Supplementary Tables S1 and S2). The highest concentration was 2.30 particles per 100 g dry sediment with the lowest concentration <0.001 particles per 100 g of dry sediment. The majority of the samples, 85%, were under 0.10 particles per 100 g of sediment (Fig. 3)
Fig. 3.

Although the particle counts were relatively low, several spatial characteristics were evident with the data. The average particle count per 100 g of sediment in the 29 identified urban locations was 0.60, with a slight increase in the 11 Ottawa/Gatineau urban area locations. The northern end of Lake Temiskaming (the wider part of the lake) demonstrated an average of 0.74 particles per 100 g of sediment from nine samples, slightly higher than the overall average. For these comparisons, a t-test was also conducted to highlight if there was any statistical difference between urban and non-urban locations (including comparing Ottawa/Gatineau sample points to the rest of the sample points), and between Lake Temiskaming and the other river locations. These three t-tests were not significant. However, a t-test was performed between tributary locations (an average of 0.25 particles per 100 g of sediment) and the main channel of the river (0.64 particles per 100 g of sediment), and the difference in concentration was significant with a p-value of <0.001.
The final counts of each location were added to a Google map, where the Community Scientists could access to explore the results, while comparing other locations to their own throughout the watershed. Additionally, a presentation was given to the Community Scientists where the research team talked about the process and the results to the Riverwatcher members, while giving input and evaluating the process as a whole.
Discussion
Particle concentration was relatively low when compared to previous studies of concentrations in freshwater sediments. For example, the collection methodology was based off Horton et al. (2017), and dry sediment concentrations on the Thames River and tributaries in the United Kingdom presented an average concentration of 66 (±7.7) particles per 100 g and a minimum value of 18.5 (±4.5) per 100 g, with the equivalent maximum value in the current research of 2.30 particles per 100 g and a minimum of 0.07 particles per 100 g. Lake Ontario in Canada presents an even larger disparity, with Ballent et al. (2016) reporting values consistently over 50 particles per 100 g, with a maximum of approximately 2 800. Even previous research on the Ottawa River highlights higher concentrations, except in underwater or wet sediments, where Vermaire et al. (2017) notes a concentration of 22 particles per 100 g at Petrie Island in Ottawa, Ontario. One Community Scientist sampled at this location and the dry sediment nearshore concentration was 0.50 particles per 100 g. Furthermore, the Ottawa River drains into the Saint Lawrence River in Quebec and Crew et al. (2020) noted a mean wet sediment concentration of 83.2 (±15) particles per kg with values reported between 6.5 and 756.2 particles per 100 g of sediment.
Several factors could contribute to the large difference in values. As highlighted, wet sediment concentrations under the water in Canadian freshwater river systems tend to present much higher concentrations than those reported in the current research. This can indicate the shoreline is not a substantial sink of microplastics in the Ottawa River watershed. This is in agreement with previous research, with Leslie et al. (2017) suggesting fibres do not tend to settle in river sediments as often as fragments. Additionally, the constant rise and fall of river water can displace microplastics from sediments (Hurley and Nizzetto 2018) and subsequently move them to the water column, sending microplastics further downstream to settle again, or even transported to marine environments. This is relevant in the Ottawa River watershed especially as the Ottawa River experiences two peak flows during the spring freshet season downstream and one peak flow upstream, due to the pattern of spring melts in the river basin and the unregulated inputs from the tributaries. This may move and (or) remove shoreline microplastics. With such a large dynamic river system, the lessened potential for microplastic deposits settling for a significant amount of time could render shoreline microplastic deposits an insignificant microplastic sink.
While examining other river watersheds and comparing to the Ottawa River, watershed size, the population base, and river discharge rates are important factors to consider. Previous research on microplastic concentration in sediment in the Thames River (Horton et al. 2017) and the Atoyac River in Mexico (Shruti et al. 2019) is compared to the Ottawa River in Table 1. Additionally, the Ottawa River watershed is in constant seasonal flux (more than rivers in more temporal zones, for example) making microplastic deposition on shorelines a dynamic and constantly changing phenomenon.
Table 1.
River Name | Approximate population in the watershed (million) | Approximate watershed size (km2) | Average river flow (m3/s) | Average concentration (per 100g) |
---|---|---|---|---|
Thames River, England | 13 | 12 935 | 65 | 66 (± 7.7) |
Atoyac River, Mexico | 2 | 4 135 | 440 | 113 (± 7.28) |
Ottawa River, Canada | 2 | 140 000 | 1 950 | 0.06 |
The only statistically significant spatial pattern to draw from the results in the community science project was the difference in concentration along the main river channel compared to the tributary locations. Generally, the tributaries of the watershed do present lower population bases compared to the main channel, where the majority of the population of the watershed resides. However, comparing the urban areas to the average particle concentration did not present any obvious spike, which could further demonstrate dry sediments are not a significant sink in the watershed. This presents the need to examine wet sediments of the watershed at a larger scale to evaluate the potential as a microplastic sink, and the need to gather more information on the significance of microplastic contamination in underwater sediments of a large watershed
Evaluating the community science methodology
With a well-planned methodology and sampling, community science can provide a spatial coverage that would otherwise be more time consuming and difficult for a research team. Furthermore, the research team has greater control over QA/QC in laboratory processing as they receive the samples from the field and can follow set protocols to minimise the potential of contamination during sample processing, which would be complicated for Community Scientists to complete without specialised equipment and training. However, sampling for microplastics in sediments did pose some difficulties and potential obstacles to address if subsequent community science projects attempt to use similar protocols as in the current research.
In such a large watershed, it is ideal to sample as much shoreline sediment as possible at each location, as the Ottawa River has many large beaches throughout the watershed, and it is important to obtain a good representative sediment sample. However, the volume of sediment processed can be an arduous task. The amount of sediment requested for each location must be balanced with the potential processing time in the laboratory, especially with time consuming sample preparation, density separation and sample inspection (including chemical analysis). These factors must be carefully considered in the project design as they can impact the practicability of a potential sediment microplastic community science project.
One of the limitations to the current research was the lack of a direct comparison of sampling as a validation to the Community Scientist samples. The research team evaluated the sampling protocol before the Community Scientists used the methodology to collect their samples. However, one improvement to the research methodology would be for the research team to sample concurrently with the Community Scientists, with an adequate number of samples to enable enough data for comparison and validation of the community science methodologies.
Another consideration with the current research is that it has mirrored previous community science project design for freshwater plastic pollution sampling, where there is only a contributory focus for the Community Scientists (Cook et al. 2021). This is where the projects are designed by scientists while the members of the public primarily contribute data. This enables the research team to have more control over QA/QC through various, often strict, sample processing protocols. Nonetheless, there has been suggestions that the path forward to fully realise the full benefits of community science is to adopt a more collaborative approach (Buytaert et al. 2014; Cundill and Fabricius 2009; Haklay 2013). This approach for community science in freshwater microplastic research empowers the Community Scientist to be involved in sampling, processing, analysing, and even disseminating the results. This would be the next logical step to increase community science capacity, while potentially presenting community science as a viable, mainstream option to research teams in microplastic research.
Conclusions
Community science programs provide an advantage to microplastic monitoring and sampling, especially in large watersheds where spatial scales are large. With robust project design and implementation, established community science or volunteer networks within watersheds can provide spatial monitoring in addition to local knowledge, advocacy while being engaged in the watershed and the issues that may affect their place of residence or vacation. However, monitoring for microplastics in dry sediments in a large watershed does present disadvantages. As beaches and shorelines in the Ottawa River watershed can be large, obtaining representative sediment samples can be difficult. Increasing the target amount of sampled sediment can be an option, however, this compromise increases sample preparation and analysis time in addition to potentially creating issues transporting large amounts of sediments to laboratories for analysis.
The results of the research presented comparatively low particle concentrations when compared to previous research in freshwater sediments. This would suggest in the Ottawa River watershed that microplastics in shoreline sediments are not a significant sink. Further research is needed to establish the potential role of wet or underwater sediments as microplastic sinks in the watershed.
Community science has provided a useful tool in expanding spatial coverage for microplastic monitoring in the Ottawa River watershed, however, careful research design and implementation are critical for successful implementation and to ensure research integrity. It is recommended that for future community science projects focussing on microplastic sampling in large watersheds, there is a necessity to develop large volume water sampling methods conducive to community science sampling projects. Furthermore, for sampling sediments, there needs to be an expansion to include sampling wet sediments and to evaluate methodologies that can be implemented for Community Scientists. Currently, community science in microplastic research still only focuses on a contribution approach, where Community Scientists only sample and contribute these samples to the researcher for analysis. For community science to expand further while contributing useful and valid data, it is essential to design methodologies where the Community Scientist is collaborative, involved in sample processing, data analysis and even data dissemination. This can increase community science capacity in Canada while potentially creating monitoring and watch programs where Community Scientists become an integral part of the research.
Acknowledgements
The authors would like to thank the Riverwatchers whose curiosity and enthusiasm were the drivers for the project’s success. Without a dedicated team of volunteers, a community science project of this scale would not be possible. The authors would also like to acknowledge the two anonymous reviewers whose constructive comments helped improve the quality of the manuscript.
Competing interest statement
The authors declare there are no competing interests.
References
Ballent A, Corcoran PL, Madden O, Helm PA, and Longstaffe FJ. 2016. Sources and sinks of microplastics in Canadian Lake Ontario nearshore, tributary and beach sediments. Marine Pollution Bulletin, 110(1): 383–395.
Barnes DKA, Galgani F, Thompson RC, and Barlaz M. 2009. Accumulation and fragmentation of plastic debris in global environments. Philosophical Transactions of the Royal Society B: Biological Sciences, 364(1526): 1985–1998.
Barrows APW, Christiansen KS, Bode ET, and Hoellein TJ. 2018. A watershed-scale, community science approach to quantifying microplastic concentration in a mixed land-use river. Water Research, 147: 382–392.
Bergmann M, Gutow L., and Klages M. (eds.) 2015. Marine Anthropogenic Litter (1st ed. 2015). Springer International Publishing Imprint: Springer.
Bonney R, Shirk JL, Phillips TB, Wiggins A, Ballard HL, Miller-Rushing AJ, et al. 2014. Next Steps for Community Science. Science, 343(6178): 1436–1437.
Bujaczek T, Kolter S, Locky D, and Ross MS. 2021. Characterization of microplastics and anthropogenic fibers in surface waters of the North Saskatchewan River, Alberta, Canada. FACETS, 6(1): 26–43.
Burgess HK, DeBey LB, Froehlich HE, Schmidt N, Theobald EJ, Ettinger AK, et al. 2017. The science of community science: Exploring barriers to use as a primary research tool. Biological Conservation, 208: 113–120.
Buytaert W, Zulkafli Z, Grainger S, Acosta L, Alemie T. C, Bastiaensen J, et al. 2014. Community science in hydrology and water resources: Opportunities for knowledge generation, ecosystem service management, and sustainable development. Frontiers in Earth Science, 2.
Castañeda RA, Avlijas S, Simard MA, and Ricciardi A. 2014. Microplastic pollution in St. Lawrence River sediments. Canadian Journal of Fisheries and Aquatic Sciences, 71(12): 1767–1771.
Cole M, Lindeque P, Halsband C, and Galloway TS. 2011. Microplastics as contaminants in the marine environment: A review. Marine Pollution Bulletin, 62(12): 2588–2597.
Conrad CC, and Hilchey KG. 2011. A review of community science and community-based environmental monitoring: Issues and opportunities. Environmental Monitoring and Assessment, 176(1–4): 273–291.
Cook S, Abolfathi S, and Gilbert NI. 2021. Goals and approaches in the use of community science for exploring plastic pollution in freshwater ecosystems: A review. Freshwater Science, 40(4): 567–579.
Corcoran PL, Norris T, Ceccanese T, Walzak MJ, Helm PA, and Marvin CH. 2015. Hidden plastics of Lake Ontario, Canada and their potential preservation in the sediment record. Environmental Pollution, 204: 17–25.
Crew A, Gregory-Eaves I, and Ricciardi A. 2020. Distribution, abundance, and diversity of microplastics in the upper St. Lawrence River. Environmental Pollution, 260: 113994.
Crichton EM, Noël M, Gies EA, and Ross PS. 2017. A novel, density-independent and FTIR-compatible approach for the rapid extraction of microplastics from aquatic sediments. Analytical Methods, 9(9): 1419–1428.
Cundill G, and Fabricius C. 2009. Monitoring in adaptive co-management: Toward a learning based approach. Journal of Environmental Management, 90(11): 3205–3211.
Forrest SA, Bourdages MPT, and Vermaire JC. 2020. Microplastics in Freshwater Ecosystems. In Handbook of Microplastics in the Environment. Edited by T. Rocha-Santos, M. Costa and C. Mouneyrac, pp. 1–19. Springer International Publishing.
Forrest SA, Holman L, Murphy M, and Vermaire JC. 2019. Community science sampling programs as a technique for monitoring microplastic pollution: Results, lessons learned and recommendations for working with volunteers for monitoring plastic pollution in freshwater ecosystems. Environmental Monitoring and Assessment, 191(3): 172.
Gillett DJ, Pondella DJ, Freiwald J, Schiff KC, Caselle JE, Shuman C, et al. 2012. Comparing volunteer and professionally collected monitoring data from the rocky subtidal reefs of Southern California, USA. Environmental Monitoring and Assessment, 184(5): 3239–3257.
Haklay M. 2013. Community Science and Volunteered Geographic Information: Overview and Typology of Participation. In Crowdsourcing Geographic Knowledge Edited by D. Sui, S. Elwood and M. Goodchild. Springer Netherlands. pp. 105–122.
Horton AA, Svendsen C, Williams RJ, Spurgeon DJ, and Lahive E. 2017. Large microplastic particles in sediments of tributaries of the River Thames, UK – Abundance, sources and methods for effective quantification. Marine Pollution Bulletin, 114(1): 218–226.
Hurley RR, and Nizzetto L. 2018. Fate and occurrence of micro(nano)plastics in soils: Knowledge gaps and possible risks. Current Opinion in Environmental Science and Health, 1: 6–11.
Hurley RR, Woodward JC, and Rothwell JJ. 2017. Ingestion of Microplastics by Freshwater Tubifex Worms. Environmental Science and Technology, 51(21): 12844–12851.
Kalpakjian S, and Schmid SR. 2008. Manufacturing processes for engineering materials. 5th edition. Pearson Education, New Jersey.
Lebreton LCM, van der Zwet J, Damsteeg J-W, Slat B, Andrady A, and Reisser J. 2017. River plastic emissions to the world’s oceans. Nature Communications, 8(1): 15611.
Lechthaler S, Hildebrandt L, Stauch G, and Schüttrumpf H. 2020. Canola oil extraction in conjunction with a plastic free separation unit optimises microplastics monitoring in water and sediment. Analytical Methods, 12(42): 5128–5139.
Leslie HA, Brandsma SH, van Velzen MJM, and Vethaak AD. 2017. Microplastics en route: Field measurements in the Dutch river delta and Amsterdam canals, wastewater treatment plants, North Sea sediments and biota. Environment International, 101: 133–142.
Mani T, Frehland S, Kalberer A, and Burkhardt-Holm P. 2019. Using castor oil to separate microplastics from four different environmental matrices. Analytical Methods, 11(13): 1788–1794.
Masura J, Baker J, Foster G, and Arthur C. 2015. Laboratory Methods for the Analysis of Microplastics in the Marine Environment: Recommendations for quantifying synthetic particles in waters and sediments. NOAA Marine Debris Division Silver Spring, MD pp. 31.
Moore CJ. 2008. Synthetic polymers in the marine environment: A rapidly increasing, long-term threat. Environmental Research, 108(2): 131–139.
Napper IE, Davies BFR, Clifford H, Elvin S, Koldewey HJ, Mayewski PA, et al. 2020. Reaching New Heights in Plastic Pollution—Preliminary Findings of Microplastics on Mount Everest. One Earth, 3(5): 621–630.
Ottawa Riverkeeper. 2021. Watershed Facts. Ottawa Riverkeeper. [online]: Available from ottawariverkeeper.ca/watershed-fact/
Peng X, Chen M, Chen S, Dasgupta S, Xu H, Ta K, et al. 2018. Microplastics contaminate the deepest part of the world’s ocean. Geochemical Perspectives Letters, 1–5.
Prata JC, da Costa JP, Duarte AC, and Rocha-Santos T. 2019. Methods for sampling and detection of microplastics in water and sediment: A critical review. TrAC Trends in Analytical Chemistry, 110: 150–159.
Reisser J, Shaw J, Hallegraeff G, Proietti M, Barnes DKA, Thums M, et al. 2014. Millimeter-Sized Marine Plastics: A New Pelagic Habitat for Microorganisms and Invertebrates. PLoS ONE, 9(6): e100289.
Shruti VC, Jonathan MP, Rodriguez-Espinosa PF, and Rodríguez-González F. 2019. Microplastics in freshwater sediments of Atoyac River basin, Puebla City, Mexico. Science of The Total Environment, 654: 154–163.
Stolte A, Forster S, Gerdts G, and Schubert H. 2015. Microplastic concentrations in beach sediments along the German Baltic coast. Marine Pollution Bulletin, 99(1–2): 216–229.
Tunnell JW, Dunning KH, Scheef LP, and Swanson KM. 2020. Measuring plastic pellet (nurdle) abundance on shorelines throughout the Gulf of Mexico using Community Scientists: Establishing a platform for policy-relevant research. Marine Pollution Bulletin, 151: 110794.
Vermaire JC, Pomeroy C, Herczegh SM, Haggart O, and Murphy M. 2017. Microplastic abundance and distribution in the open water and sediment of the Ottawa River, Canada, and its tributaries. FACETS, 2(1): 301–314.
Wagner M, and Lambert S. 2018. Freshwater microplastics: Emerging environmental contaminants? Springer Berlin Heidelberg.
Supplementary material
Supplementary Material 1
- Download
- 33.24 KB
Supplementary Material 2
- Download
- 4.60 MB
Information & Authors
Information
Published In
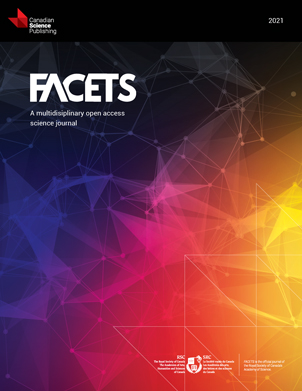
FACETS
Volume 8 • Number 1 • January 2023
Pages: 1 - 15
Editor: Irene Gregory-Eaves
History
Received: 28 April 2022
Accepted: 7 September 2022
Version of record online: 5 January 2023
Copyright
© 2023 Forrest et al. This work is licensed under a Creative Commons Attribution 4.0 International License (CC BY 4.0), which permits unrestricted use, distribution, and reproduction in any medium, provided the original author(s) and source are credited.
Data Availability Statement
Data generated or analyzed during this study are provided in full within the published article and its supplementary materials.
Key Words
Sections
Subjects
Plain Language Summary
Community Scientists Sampling for Microplastics in River Sediments of the Ottawa River
Authors
Author Contributions
SAF conceived and designed the study.
KA and LH performed the experiments/collected the data.
JCV analyzed and interpreted the data.
KA, LH, and JCV contributed resources.
KA, LH, and JCV drafted or revised the manuscript.
Funding Information
The authors declare no specific funding for this work.
Metrics & Citations
Metrics
Other Metrics
Citations
Cite As
Shaun A. Forrest, Katherine Alambo, Larissa Holman, and Jesse C. Vermaire. 2023. Evaluating community science sampling for microplastics in shore sediments of large river watersheds. FACETS.
8: 1-15.
https://doi.org/10.1139/facets-2022-0104
Export Citations
If you have the appropriate software installed, you can download article citation data to the citation manager of your choice. Simply select your manager software from the list below and click Download.
Cited by
1. The hidden threat of microplastics in urban freshwater ecosystem: A comprehensive review